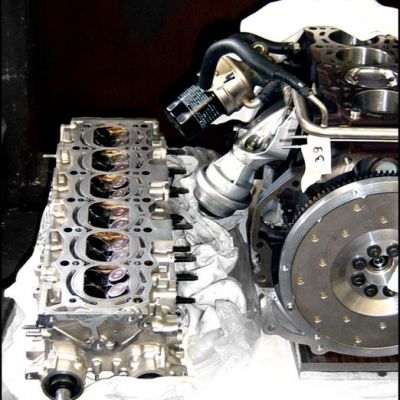
Das Projekt "Pitch Black Supra" begann Anfang 2004 mit einer Frage: Wie baut man eine Fahrmaschine mit 800PS, die trotzdem so robust und alltagstauglich ist wie das Serienmodell ?
Klar, dass die Antwort lautete: "Mit einem haltbaren Motor".
So kam es, dass für dieses Projekt nur ausgewählte Komponenten durch Christian Lutosch (Underground-Racing) direkt aus den USA importiert wurden. Neben bekannten Marken wie JE Pistons, Pauter, Clevite77 oder ARP kamen aber auch Eigenentwicklungen wie die SSE Nockenwellen oder die Shim-under-Bucket Conversion zum Einsatz, die eine spätere Drehzahlanhebung auf bis zu 9.000 U/min ermöglichen.
Für den Motor Ein- und Ausbau waren wir selbst verantwortlich. Mit den Tipps von Christian und der Hilfe eines KFZ-Mechanikers, als auch der Zuhilfenahme der Werkstattbibel, war es nicht unbedingt ein unlösbares Problem.
Schon am ersten Tag war der Motor draußen. Auch wenn jeder Stecker anders ist, jeder Schlauch seine genaue Länge hat um nur an einer Stelle zu passen und somit eigentlich ein falsches wiederanschliessen fast schon unmöglich ist, wurden nichts desto trotz vorsichtshalber alle getrennten Leitungen nummeriert.
Angefangen mit dem Ausbau der Auspuffanlage und der Kardanwelle, gab es 2 Möglichkeiten den Motor auszubauen: Komplett mit Getriebe oder ohne Getriebe.
Beim 2ten Weg (der auch gewählt wurde) musste eine extra Schlüsselverlängerung angefertigt werden, damit man an die oberen Getriebeschrauben zum Motor gelangen konnte.
Nachdem auch das Getriebe abgeschraubt war, wurde der Motor raus gefischt.
Ausgebauter Motor & Turbosystem
Das Abmontieren der Anbauteile wie dem Turbosystem ist bei ausgebautem Motor natürlich wesentlich leichter. Hier heißt es nur Schraube für Schraube und Teil für Teil ab.
Das EFI System hingegen wurde im eingebauten Motorzustand abmontiert, da unter dem Einlasskrümmer relativ viele Verbindungen vorhanden sind.
Selbstverständlich sollte man nichts desto trotz immer das Werkstattbuch zu Hilfe nehmen.
So ist es z.B. wichtig, die Nockenwellenschrauben in der richtigen Reihenfolge zu lösen !
Die Instandsetzung
Nach dem abmontieren des Motorkopfes konnte man sich die ersten Eindrücke des Motorinnenlebens machen.
Unglaublich: Selbst nach den 200.000 gelaufenen km war noch der original Hohnschliff an den Zylindern wie neu. Dieser feine Schliff ist dazu da, damit sich im Betrieb des Motors das Öl optimal an den Zylinderwänden verteilen und nicht leicht reißen/abgerieben werden kann.
Somit ist der Motorblock und der Zylinderkopf für den Instandsetzer vorbereitet.
Folgende Arbeiten wurden vom Instandsetzer durchgeführt:
- Block und Zylinderkopf werden auseinander gebaut
- Block und Kopf werden dampfgereinigt / gewaschen
- Block und Kopf werden geplant und geschliffen
- Die Installation wird vorbereit
- Zylinder mit der Verwendung der Torque Platte neu gehohnt
- Kurbelwelle auf Haarrisse geröntgt und vermessen
- Ventile reinigen und und ggf. einschleifen
- Einbau der neuen Komponenten in den Block / Kopf
Für den (reinen) Motor wurden folgende neue Komponenten verwendet:
- Toyota komplettes Dichtungsset Motor 2JZ
- HKS 1.4mm STOPPER Metall-Zylinderkopfdichtung
- JE Schmiedekolben
- JE Kolbenringe
- Clevites KW Lager
- Clevite Pleullager
- Pauter Schmiedepleuel
- ARP U/C Kopfbolzen
- ARP Kurbelwellenbolzen
- SSE 272 scharfe Nockenwellen
- SSE Shims under Bucket Conversion
- Unorthodox Racing Cam Gears
- GReddy Zahnriemen
Da man vor der Instandsetzung nicht sagen konnte, wie gut noch der alte Hohnschliff ist, wurden JE Übermasskolben bestellt und benutzt. (Daten werden noch nachgereicht) Da die JE Schmiedekolben aus Aluminium bestehen, ist deren Materialeigenschaften wesentlich anders, als die der original Toyota Kolben. So dehnen sich Schmiedekolben bei Hitze wesentlich mehr aus als andere. Für die Schmiedekolben müssen daher wesentlich größerer Werte verwendet werden.
Beim Aufbau eines (Renn)Motors muss entscheiden werden, ob man später nur Wert auf viel Leistung legt oder aber auch einen langlebigen Motor haben will. Je höher die Leistung umso höher auch die Materialbelastung.
Bei sehr hoher Leistung muss Rennsprit verwendet werden. Bei unserem Tankstellensprit ist eine Leistung von ca 600 - 700 PS an der Kurbelwelle möglich. Danach fängt der Motor an zu klopfen, weshalb man mehr Oktan fahren muss. Bei der Verwendung eines anderen Sprits herrschen u.a auch höhere Temperaturen.
Im Klartext heißt dies, dass für einen Rennmotor mit über 800 PS ein wesentlich größerer Ringgap verwendet werden muss. Bei über 1000 PS wird dieser noch größer und so war auch die tabellarische Auflistung auf dem Zettel der JE Kolben. Man kann also nicht in einem Moment einfach einen 330 PS Motor fahren und im anderen Moment einen 1000 PS.
Bei einem zu gering eingestellten Ringgap kann sich bei hoher Hitze der Ring komplett schließen und somit anfangen an der Zylinderwand zu schleifen. Der Verschleiß hier ist sehr hoch. Ein zu groß eingestellter Ringgap hat zur Folge, dass der Ölverbrauch wesentlich höher als normal ist und schlimmstenfalls ein Kolbenkipper den Motor zerstören kann.
Entschieden wurde bei diesem Motor für einen Ringgap für ca 800 PS.
Für den Zylinderkopf wurden wieder die original Ventile und Ventilfeder verwendet. Eine Drehzahlanhebung war bis dato nicht geplant, auch wäre für die geplante Leistung von 600 - 800 PS an der Kurbelwelle mit dem passenden Singleturbo keine Drehzahlanhebung notwendig.
Rückwirkend kann ich nun sagen, dass mit dem derzeit verwendeten PHR (T67) Turbolader der Fullboost von 1,1 Bar bereits bei 3800 Umdrehungen anliegt. Man kann die Leistung also noch weitere >3000 Umdrehungen ausfahren. Bei einer Leistung von über 1000 PS wäre zB ein großer Turbolader (z.B. T88) notwendig, welcher erst ab ca 5000 - 5500 Umdrehungen den vollen Ladedruck erreicht.
Eine Drehzahlanhebung ist hier selbstverständlich empfehlenswert, da man mit dem restlichen Drehzahlband diese Leistung kaum wird ausfahren können.
Für den Zylinderkopf wurden lediglich andere (scharfe) Nockenwellen und andere Ventilkappen verwendet.
Die Funktion der anderen Ventilkappen ist leicht erklärt.
Während man original das Ventilspiel an den oberen "Plättchen" (Shims) einstellen muss, werden bei dem "Shims under Bucket" System diese unter der Kappe verwendet.
Mal abgesehen davon, dass dieses System im Vergleich zu dem original System wesentlich leichter ist, so bewegen sich die Nockenwellen nun nicht mehr auf dem Einstellplättchen (Shims), sondern direkt auf der ganzen Kappe (Bucket).
Wesentlich höhere Drehzahlen sind zumindest in diesem Bereich möglich.
Jedes Shim (das kleine Stück rechts auf dem Foto) musste natürlich passend zu den Ventilen eingeschliffen werden. So war der untere Bereich viel zu lang und es bestand die Gefahr, dass das Shim gleich beim ersten Motorstart die Ventilkeilen raus drücken würde.
Somit wurde die Höhe des Shim unter der Berücksichtigung der Materialausdehnung um 1,5 mm gekürzt, sodass zwischen dem Shim und der Ventilkeile ein Spalt von 0,15 mm besteht.
Das relativ zeitraubende und komplizierte einstellen des Ventilspiels mit dem neuen System werde ich später noch erklären.
Der instandgesetzte Motor
Nachdem der Instandsetzer die oben genannten Punkte abgearbeitet hat, kamen der Zylinderkopf und der Motorblock wieder in die Werkstatt.
Selbstverständlich sollte bei einer solchen Instandsetzung eine neue Öl und Wasserpumpe eingebaut werden.
Statt der original 2-Mass Schwungscheibe wurde nun eine Fidanza 1-Mass Schwungscheibe eingbaut. Diese ist um ca die hälfte leichter. Durch das verringern der rotierenden Masse hat man ein wesentlich besseres Ansprechverhalten des Motors.
Zusammenbau und Einbau
Etwas zu zerlegen ist relativ einfach und mit einem Hammer sogar schnell gemacht.
Etwas wieder zusammen zu bauen schon etwas komplizierter.
Und das war es auch hier.
Angefangen von unten mit der Anbringung des Ölwannentrichters und der Ölwanne, bishin zu dem Motordämfern
Zur Info: Die Silikondichttube kostet bei Toyota stolze 70 Euro.
Wieder auf den Beinen, sollte der Zylinderkopf an den Block befestigt werden, doch dann der Schock. Eines der aus den USA importierten ARP-Mutter hatte kein Gewinde und einen weiteren Ersatz hierfür gab es nicht. Unglaublich aber wahr.
Nachdem festgestellt wurde, dass es auch noch kein metrisches sondern ein Inch Gewinde war, sahen wir den Zusammenbau des Motors für gescheitert.
Es blieb nichts anderes übrig, als ein Risiko einzugehen und das Gewinde einzuschneiden.
So wurde die Mutter zu einer Fach Firma gebracht, welche sich dran versuchte. Es gab nur einen Versuch
"Was ist das für ein Material", fragte mich der Facharbeiter, nachdem beim ersten Versuch ihm gleich das Messer in der Maschine gebrochen war. Beim 2ten Versuch fing das Messer an zu vibrieren, sodass das Gewinde in ca 100 Gängen eingeschnitten wurde.
(rechts) Nun konnte der Zylinderkopf endlich befestigt werden. Eingebaut sind hier auch schon die "Shims under Bucket"
Die Kleinigkeiten
Noch während der Motor beim Instandsetzer war, habe ich mich etwas mit der Bremsanlage beschäftigt, denn es mußten neue Bremsklötze rein.
Bei dieser Gelegenheit habe ich Bremssättel optisch etwas aufpoliert.
Nachdem diese sandgestrahlt wurden, habe ich sie mit ATU hitzebeständiger Farbe besprüht.
Ebenso wurde während dieser Zeit das Turbosystem auseinander gebaut. Da ich bei Beschleunigungen auf der Autobahn gelegentliche Aussetzer des 2ten Turboladers hatte, wollte ich nachschauen, in welchem Zustand sich dieser befindet.
Der 2te Turbolader hatte einen kleinen Riss im inneren des Abgasgehäuses. Viel repariert werden konnte hier nicht mehr, lediglich ein neuer Turbo würde etwas bringen.
Da aber ein Singleumbau geplant war, wurden die Turbos lediglich einer Firma zur Reinigung und Aufpolierung weggegeben. Halten sollte der Turbolader noch locker paar weite Kilometer.
Ventilspiel
Das einstellen des Ventilspiels ist eine zeitraubende Geschichte.
Nachdem die Shims und die Buckets auf die Ventile gesetzt werden, wird die Nockenwelle von oben eingesetzt und in der richtigen Reihenfolge mit dem richtigen Drehmoment befestigt.
Das Ventilspiel wird mit einer Fühlerlehre gemessen.
Dabei muß bei dem aktuell gemessenen Ventil die Nockenführung nach oben zeigen. Dh. das Ventil muß geschlossen und im höchsten Punkt sein.
Die Werte beim kalten Motor sind:
Einlass: 0,15 - 0,25 mm
Auslass: 0,25 - 0,35 mm
Damit die Nockenwelle für jedes vermessen des einzelnen Ventilspieles gedreht werden konnte, mußte das Nockenwellenrad ebenfalls angebracht werden.
Hinweis: Zumindest bei den einstellbaren Unorthodox Nockenwellenräder müssen die Einstellschrauben mit einem Kleber zusätzlich befestigt werden. Dies hatte ich aus Unwissenheit nicht getan, sodass sich die Nockenwelle nach den ersten 150 km von alleine sich um 1 cm verstellt hat. Das der Motor nicht mehr rund lief, versteht sich)
Mit dem Zahnriemen wurde dann die Nockenwelle per Hand gedreht. Das Anspannen des Zahnriemens an die Kurbelwelle war nicht notwendig, da der 2JZ ein Freiläufer ist und somit die Ventile nie auf die Kolben aufschlagen können.
Nach dem abmessen und notieren jedes einzelnen Ventilspiels auf einer Seite, mußte die Nockenwelle zum einschleifen der Shims wieder erneut abgebaut werden.
Da die Shims wesentlich größer waren als notwendig, mußte bei jedem die obere Schicht abgetragen werden.
Abgemessen und Abgeschliffen werden diese wieder erneut mit der Nockenwelle eingebaut und das Ventilspiel wird erneut im gleichen Prozedere gemessen.
Die Nockenwellen und Nockenwellenlager, ggf. auch die Ventilbuchsen sollten beim Einbau etwas mit Öl gefettet werden.
Das Einstellen kann relativ lange dauern, da man einen perfekten Wert auf Anhieb nicht hinkriegt.
Zu wissen ist, dass ein zu grosses Ventilspiel nicht so tragisch ist wie ein zu klein eingestelltes Ventilspiel. Bei einem zu grossen Spiel werden diese lediglich etwas klappern. Ein zu klein eingestelltes Ventilspiel kann dazu führen, dass die Ventile verbrennen können.
Nachdem das Ventilspiel eingestellt wurde, konnte alles wieder nach und nach eingebaut werden. Das Turboladersystem wurde wieder zusammengebaut und an den Block befestigt (hier natürlich auch die Reihenflolge und das Drehmoment beachten), sowie die KW Scheibe, die Wasserpumpe oder das Spannrad.
Wichtig: Bei jedem Ölpumpenwechsel muß diese entlüftet werden. Hierfür dient eine Öffnung in der Ölpumpe, in welche Öl nachgefüllt werden muß. Geschieht das nicht, wird die Ölpumpe lediglich Luft pumpen und der Motor geht beim ersten Lauf nach wenigen Minuten kaputt.
Ein normales Auffüllen des Öl in den Motorraum entlüftet nicht die Ölpumpe !
Hier wurde derzeit noch ein original Nockenwellenrad eingebaut, da das zweite Unorthodox Nockenwellenrad noch nicht aus den USA gekommen war.
Rein damit
Nachdem nun alle Kleinteile (bis auf das EFI - System) an den Block befeistigt worden sind, konnte der Motor nun endlich wieder rein.
Während unten wieder das Getriebe, die Kardanwelle und die original Auspuffanlage wieder angeschraubt wurden, schraubte und steckte man oben alle vorher nummerierte Stecker und Schläuche zusammen.
Dies ging sogar relativ schnell und leicht.
Die entscheidende Minute
Nun ist zumindest theoretisch alles wieder eingebaut und angeschlossen, alles nochmal erneut durchgedacht und durchgecheckt, lose Stecker und Schläuche gesucht. Alles soweit in Ordnung und theoretisch wurde trotz Hürden alles richtig gemacht.
Es wurden dann alle Flüssigkeiten nachgefüllt. Kühlflüssigkeit, Motoröl, Bremsflüssigkeit, Servolenkungflüssigkeit.
Das Bremssystem wurde entlüftet.
Das Servolenkungssystem durch das anstrengende hin und her drehen der Lenkung bis zum Anschlag ebenso entlüftet.
Mit der Knarre wurden ein paar Runden an der Kurbelwelle gedreht, damit sich das Motoröl im System zumindest schon verteilen kann.
Wieder wurde erneut Öl nachgeprüft und nachgefüllt.
Danach wurden die Drosselklappenstecker und sicherheitshalber auch die entsprechenden Sicherung gezogen, damit der Motor beim einschalten auf gar keinen Fall startet. So wurden mit dem Anlasser ebenso ein paar Runden im Motor gedreht und auch die Benzinleitungen wurden dadurch geflutet und haben wieder Druck bekommen.
Nun also hieß es den Motor zum ersten mal zu starten. Meine Knie waren dafür einfach viel zu weich und ich wollte es nicht machen. Ich war mit vielen Horrorszenarien im Kopf einfach nicht in der Lage dies zu machen.
So hatte der Sohn des Mechanikers die Mission den ersten Motorstart durchzuführen, während ich 10 Meter weiter mit Angst und Bange rumstand.
Es gab 4 mögliche Szenarien.
- Der Wagen springt beim ersten Start gleich an und läuft
- Der Wagen zündet nicht und nur der Anlasser dreht.
- Der Wagen springt kurz an und geht wieder aus
- Der Wagen springt an und geht kaputt (Kolben, die Shims under Bucket, o.ä.)
Je tiefer man in die Auflistung der Szenarien fällt, desto schrecklicher wäre es. Die Stecker zum EFI und die Sicherungen wurden wieder eingesteckt. Punkt 23 Uhr war es dann so weit und der Mechaniker sagte zu seinem Sohn
"Starte"
Er dreht den Schlüssel auf ON ..... wartet ...... und zündet.
ER SPRANG GLEICH AN und läuft und läuft und läuft.
Nach ca 30 Sekunden wurde der Motor wieder aus gemacht. In den ersten paar Sekunden kam aus der Auspuffanlage etwas Rauch, was aber absolut normal ist.
Es wurde erneut das Motoröl geprüft und wieder erneut gestartet. Er lief ohne Probleme.
Da ist uns ein Stein vom Herzen gefallen.
Am restlichen Abend wurden wartungstechnisch nur noch einige Kleinigkeiten erledigt und mit einem anschließendem Feierabendbier(Kasten) beendet.
Am nächsten Tag sollte der Wagen eingefahren werden.
Das Einfahren des Motors
Über das Einfahren eines neuen Motors könnte man stundenlang philosophieren. Es gibt verschiedene Methoden und Theorien.
Die einen meinen, man sollte den Motor behutsam die ersten paar tausend Kilometer einfahren, nicht über 3000 Umdrehungen und ohne Vollgas fahren mit dem Öl, welches man später auch verwenden wird. Die anderen meinen, hierfür ein grobkörniges Mineralöl für das schnellere Einschleifen der Komponenten zu verwenden und erst ab 1000 km auf ein vollsynthetisches zu wechseln.
Eine andere Theorien zum Einfahren eines Rennmotors sagt, dass man diesen von Anfang an mit voller Belastung fahren sollte (Natürlich immer nach dem warm fahren des Motors) .Sofern der Motor gut gemacht worden ist, hält es. Wenn nicht, geht er schnell kaputt.
Beim einfahren des Motors kann es am Ende entscheidend sein, ob man einen geringen oder hohen Ölverbrauch haben wird.
Entschieden wurde für die behutsame Einfahrmethode.
Dabei wurde für die ersten 1000 km ein billiges Mineralöl verwendet.
Nach ca. 15 Minuten Laufzeit des Motors im Leerlauf wurde das Öl (wieder Mineralisches) sowie der Ölfilter gewechselt.
Man kann den Ölfilter ggf. öffnen und nach Metallpartikel absuchen.
Mit diesem Öl wurden 1000 km gefahren und dann mit einem erneuten Öl- und Filter-wechsel auf das hochwertigere synthetische Castrol RS 10w60 Öl gewechselt.
Damit wurden 4000 km gefahren.
Beim Einfahren wurde die Drehzahl von 3000 Umdrehungen nie überschritten. Ebenso wurde kaum bis gar kein Ladedruck gefahren und nicht stark beschleunigt.
Nach den 4000 km ein erneuter Öl und Filterwechsel.
Jetzt auch wurden die ARP-Kopfschrauben nachgezogen. Somit sollte der Motor eingefahren sein und man kann die Drehzahl nach und nach steigern.
Ich denke, dass dies die Beste und schonenste Methode zum Einfahren des Motors ist. Der Motor hat nun nach über 2 Jahren über 50.000 km auf dem Tacho, zwischen den Ölwechselintervallen von 10.000 km hat er einen geringen (unter 100 ml) bis keinen Ölverbrauch.
Und er läuft und läuft und läuft .....
Hoffe euch hat dieser Bericht gefallen. Konnte mich nach 2 Jahren endlich dazu durchringen, es fertig zu schreiben. Für meinen Geschmack hätte er vielleicht viel mehr technischer und detaillierter sein können, jedoch habe ich nicht mehr alle Fotos, Informationen und erst recht die Erinnerungen zum Motorumbau.
Valve Cover: 3"
Head: 4 3/4"
Block: 10 3/8"
Upper Oil Pan: 2 3/8"
Lower Oil Pan: 3 3/4"
Total Height: 24 1/4"
Block Length (top, no accessories or oil pump): 23 9/16"
Block Length: (middle, no accessories or oil pump): 24 1/4"